We can’t call this the Master Bath, because that’s back by our Master Bedroom. And we can’t call it the Guest Bath, because that’s back in the Guest Wing. However, we can’t really call it a Powder Room, either, even though that more closely resembles its function. But, because it also has a shower, it’s more than a Powder Room. So, we’ve recently stumbled on the nomenclature of “Powder Bath™”. Consider that term wholly made up by us and introduced on this site.
This room will be the last major renovation in the house…we think. It’s been hanging fire since our daughter did a test tear of the old wallpaper several years ago. The room has been a little shabby since—although wholly functional—but when Linda found a mirror at an estate sale down the street, apparently the reno clock started to run. She started pulling the wallpaper off in earnest toward the end of 2012, forcing me on a quest for materials.
I can’t even say what the timeline for the bath was, but we thought we’d have gotten to it before now. So, I went on a search to see if we could get more of the same tile as in the hall/foyer. Miracle of miracles, picking a tile store out of the phone book (metaphorical—of course I found them online), we went to the place with one of our leftovers and the proprieter matched the tile perfectly. Not only that, she pointed us in the right direction for managing thresholds.
The genesis had already been warming up—we had seen a pedestal sink we liked—at the local big box, but only online—so we went online and ordered it. The general concept, by the way, was that since the room was so small anyway, if we took out the vanity and replaced it with a small pedestal sink, it would visually enlarge the space. For the same reason, we’ll replace the toilet with a similar round nose design, low flush unit, and then make color and accessory choices to complement that mission.
But it was the mirror that started the ball rolling.
As always, click on any thumbnail for a larger image.
|
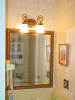 |
|
Snowball effect. New mirror—old lights sucked, ergo, new lights.
|
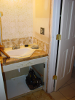 |
|
About a year later…demo begins. I’ve already removed the backsplash tiles (saving them for baseboard use later). I’m well on the way to getting the tile off the top.
|
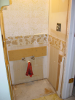 |
|
The vanity is now gone and I can begin reconstruction.
You can see, down at the floor, where the old backsplash tile I removed will be reinstalled. It’s precisely the same dimension.
|
|
The day the sink arrived was when the tools came out. We now join our demolition in progress.
|
|
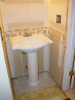 |
|
Once the vanity was gone we thought we’d see what the sink was going to look like. We’re still a long way from functionality, let alone completion, but doesn’t it look nice?
|
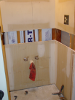 |
|
The mastic residue was far too intrusive to repair, so I cut out the backing drywall and will replace and feather in new pieces. I also need to sister some 2×4s onto the studs on the back wall for the lags which will hold the sink bowl in place—a common protocol with pedestal sinks.
|
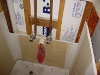 |
|
The flanges were awfully grunged up with caulk (a previous owner) and I needed more access for backing framing for the sink bowl bolts, so I cut out some more drywall. |
|
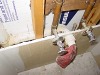 |
|
Sometimes opening up the patient yields opportunity—sometimes not. I’ll easily be able to replace the supply flanges and have plenty of pipe available to cut back for a cleaner installation. However, the waste is going to have to remain as is. Maybe I’m just lazy, but the cost/benefit ratio isn’t high enough to undertake the extra labor. |
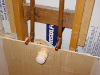 |
|
Although temporary, I ditched the rag and bought a cap for the waste connection. I pulled the valves and filed off the ferrules on the supply lines. Then I cleaned up the pipes and soldered on temporary caps. Not one, but two, soldering failures for the first time in this house reno. Good reasons for both, but not worth explaining. I cut them off and re-did them with no leaks. Note the 2×4s scabbed onto the studs—they’re for the lags which will hold the sink in place. |
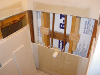 |
|
After cleaning up the waste fitting, I started fitting chunks of drywall for the openings left from surgery. I also decided to inlet the two horizontal chunks of 2× because the lag bolts were probably going to land in the gap between the studs and the scabs. |
|
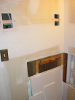 |
|
The two holes up high were where the matching towel bar had been installed. And we’re ready to rock! |
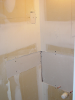 |
|
Rock in place on the left half of the vanity nook. |
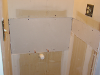 |
|
Rocking complete. Now for some serious taping and mudding. By the way, don’t hate on me for gaps and misaligned joints. First of all, tape, mud, and paint cures all ills. Secondly, it’s almost impossible to perfectly match up old work with new in this kind of project. |
|
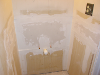 |
|
Here I’ve taped (with Fiberglas™ mesh—better for repair work) and applied the first coat of mud. Looks awful, doesn’t it? That’s why you always do three coats of mud. I’m done for the day, though—“drying” compound. |
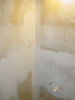 |
|
Several sessions with mud and the taping knives and I finally got to the point where I could do some sanding. You can’t really tell from the picture how good most of it looks. A little more skim coating and a little more sanding and I’ll be happy with the results. |
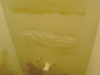 |
|
Oops. I was going along so well. Then I set the sink back in temporarily to show it off to a visitor. There was a pretty good sized gap at the top—¼" or more. See below for details. Color difference is because I shot this without flash to highlight the build-up.
|
|
I’m going to spend about a week building this up to look right but not be noticed. The gap was caused by the usual suspect—inside corners (and by the original builder)—two of which are in a very close proximity (≈30"). It didn’t matter when the vanity was in, because the backsplash tile flowed along the curve, but now, the sink bridges the two built-up corners which leaves a gap. The “week” I mentioned is because I’m using a drying compound (as opposed to a setting compound—which can be ready to sand in as little as 30 minutes). So, each layer needs at least 24 hours to dry. The good news is the later layers are much thinner and can be worked sooner.
While waiting for the paint mud to dry, I went out and bought a new exhaust fan to replace the ageing (and noisy) NuTone. When I pushed the “test” button at the big box display, I had to actually put my hand over the screen to feel that the fan was on, as I couldn’t hear it (rated at 1.5 sones). After thinking about it I began to wonder what the motive was in making bathroom fans quiet. After all, in my experience, most of the time the fan is turned on in this room is so everyone else can’t hear the visitor tinkle. Are they ever in for some embarrassment.
|
|
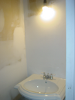 |
|
Not much to tell different from this pic and the previous above. Suffice to say I’ve sanded as much as I’m going to, and it’s time to prime. |
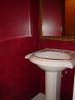 |
|
No point in showing a pic of the area primed, as it would look like a white wall. Instead, let’s show a red wall. Burgundy, actually, and no, that’s not a faux finish—that’s a paint so thick with pigment, it needs multiple coats. This is just the first. |
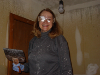 |
|
Linda wanted to contribute to the project, and removing the popcorn from the ceiling was on her list. Sadly, she doesn’t have a lot of experience working overhead. The flare on her safety glasses is mostly from the flash…fog is the rest of it. |
|
I can report the removal of the old toilet and the delivery of the new one. Life has its oddest curiosities—I set out the three porcelain pieces of the old, still functioning, albeit full flush toilet (bowl, tank, lid), fully expecting them to be gone in the am courtesy of enterprising trash day scavengers. Went out to get the morning paper, and the lid was gone—but the tank and bowl remained.
Not unexpectedly, I found that the steel flange under the toilet needs replacing, which is just as well, as I neglected to pick up the flange bolts and caps needed for the installation when I was over at the big box to get wax ring(s), supply hose, shut-off valve, and escutcheon. This also gives me time to grind down some concrete which was poorly floated around the drain. Basically, the finishers didn’t consider that someone would ever put down ceramic tile under the loo. I’ll fix that.
Okay, it’s been a few weeks—some procrastination, some different tasks, some background work on this project which doesn’t merit documentation. My principal “next step” was to trim back the hall tile to where the new threshold tile is going to go. I’d done several tests of my planned technique and felt I’d minimized the risks of damage to the remaining tile as much as possible.
Also, it was getting time to commit to getting the baseboard tile installed, which necessitated removing the mastic residue from the previous use on the old built in vanity. My tile vendor suggested I would be able to muscle it off with some sort of stiff blade, but my attempts with that plus some others with various solvents were fruitless. Ultimately, I was able to use my angle grinder (with diamond blade) and a prop of 2×4 as a thickness planer, which was not only successful, but reasonably quick, as well. I cleaned up 21 tiles and about a dozen bullnose tiles in about an hour.
|
|
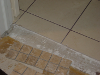 |
|
First the tile cutting. Two divots—the one on the right was an inevitability because of the technique I used. The one on the left was unexpected and I think a result of the violence used in removing the remaining tile. We’re considering them a feature for now.
|
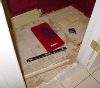 |
|
This is where I’m headed. Visible is the existing base tile, the cleaned up salvage tiles which will continue, the bull nose tile, and the existing hall floor tile. The 2×2s will be the transition between hall and bath.
|
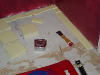 |
|
A closer view from a different angle testing the layout of the bullnose. The two side walls and about half of the back wall will be whole tiles. Where the two rows converge will be partially camoflaged by the pedestal, so using scraps shouldn’t be too noticable.
|
|
The new floor tiles have arrived—I’m slightly disappointed, as the new ones appear more porcelain than ceramic, and the color is slightly off. However, between the wall color, the fixtures, the relatively small size of the room, and the genius of our tile provider and her suggestion of the 2×2 transition tiles, I think any notion of the color difference will be overwhelmed by other stimuli. The same probably applies to the divots, as well.
I got the wet saw down out of the shop attic and picked up a bag of thinset, so sloth is now the only impediment to setting some yellow tiles (the bases). Actually, sloth only lasted a couple of days. I primed the remaining areas of drywall (an image of primered drywall is pointless) and then decided to mix up some thinset.
|
|
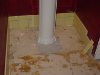 |
|
Base tiles set, pedestal temporarily in place for context. Note bullnose on back row is coped at both ends. Bullnose and square tile on right not set until I trim the door casing. Grout later. |
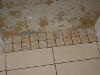 |
|
Threshold tile set in door to hall/foyer. I’m painfully aware of the divots, thank you. They were unavoidable and irreparable, except perhaps with some colored epoxy. They’re going to be a feature we won’t celebrate too exuberantly. |
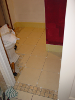 |
|
Laying out the tile so I can make cuts before actually setting them in mud. It’s going reasonably well, so far. I’ll set this lot, then do the rest of the layout the following day. Pulling the toilet and painting accompanies that stage. |
|
(21 February 2013) I’m really sensing the finish line on this project. I picked up the off-white grout today for the base tiles, which I hope to finish tomorrow. I’m going to mark the area I’ve laid out today and then set those tiles when the grout dries on the base tiles.
When the floor tiles are set as laid out above, I’ll pull the toilet and paint the whole room. Probably two coats—maybe more, based on my experience in the media room. Then I’ll lay out the rest of the floor tiles, set them in mud, replace the toilet, install the sink, and then I’m done, save for the vent and ceiling light.
|
|
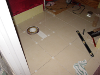 |
|
Tile set in the area depicted in the previous image. Walls also have received their first coat, as evidenced more fully in the next image. |
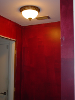 |
|
While the impact of the color on the walls is apparent in this shot, the focus is intended to be on the new light fixture that just went up. It matches the fixture which will be over the mirror. |
 |
|
I spent a lot of time agonizing over layout details. I should have spent more. Details below. |
|
Lay observers generally aren’t aware of the principles involved in laying out a tile job. They might notice if it’s pleasing or not, but they won’t know why. Two of the precepts are try to place full tiles in the most visible places and minimize narrow strips of tile—usually less-than-half widths. If one were to review the Foyer page, one could see the tile layout I wound up with there. It was a very complicated arrangement, and while it might appear I violated the less-than-half widths precept, its consideration was trumped by the two widths of the hall and the six passageway openings (front door, archway to media room, door to mechanical’s hall, door to powder bath, double door to closet, portal to library). It can be a very complex process.
In the case of the Powder Bath, my constraints included where the tile lay with regards to both the doorway and the hall tile. I wanted to honor the grout line in the hall tile, for openers, so that set the left/right position. Then, I had the choice of a full tile at the threshold or a full tile at the near back wall (the shower wall). I selected the full tile at the doorway. It wasn’t unreasonable in general terms. I still got more than a half tile at the shower wall and more than a half tile at the far back wall. The only down side anywhere was the ≈1" strip at the wall behind the sink. Since that generally would be camoflaged by the sink itself, it was acceptable.
However, if I’d spent just a little more time, I could have nudged the layout about 1½" toward the threshold—still had nearly a full tile there, had a fuller tile on both the back wall and the shower wall, and had both the toilet and the sink centered on the tiles under them. It may be that no one else will notice, but I’ll know. It’s not bad enough to tear the whole thing up, though. Just another of life’s lessons for later.
In the meantime, grouting throughout was accomplished, a hole was drilled through the new tile into the concrete slab, and a Star anchor was set for the bolt which anchors the pedestal to the floor. I installed the sink and made the supply and drain hookups, and tested. I made a run to the big box and picked up a suitable towel ring, then we argued over its location. Suffice to say, the final vote was 4–1, with an eventual capitulation to unanimous.
|
|
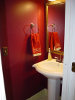 |
|
And here’s the result of the towel debate (and sink nook remodel). This is essentially a fully completed nook. We may seek out a better towel, but this one from inventory works pretty well, don’t you think? |
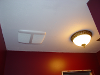 |
|
Because this room is so small, there’s no way to get this picture without all sorts of distortion. Just enjoy the new fan and the new light (second appearance) and don’t bother trying to figure out the angles. |
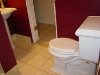 |
|
The toilet in place, with a peripheral view of the sink nook. It will be impossible to really see the two of them “together”. |
|
There’s temporarily a blank spot in the photo array above. I have to make a trip into the attic to permanently affix the fan housing to the support structure. Until I complete that, I have to hold off reinstalling the toilet becuase there’s some final messy drywall trimming to be done in the ceiling which I can’t do until the fan’s location is finally set. Then the toilet. Done.
There will be a few niggling other things to do which won’t affect the functionality of the room—rehang the door to the service hallway, for example (done), and possibly some crown molding. But the toilet will be the big thing, and it’s imminent, which will make the room fully usable again…and, there’ll be a picture. This has been a good project.
|
|