We selected the southeast bedroom as the computer room/office and added a couple of big-box RTA (ready to assemble) bookcases along with a computer desk (found at a resale shop for a ridiculous price) and the traditional file cabinets/door auxiliary work surface for printers, etc. Eventually, it became apparent that the bookcases were inadequate for a variety of reasons, so the new project was built-ins. My design idea was a floor to ceiling column on either side of the window and a half column below the window.
As always, click on any thumbnail for a larger image.
|
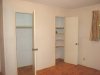 |
|
To review, the target construction zone is along the east wall to the right in this image.
|
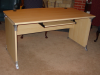 |
|
Salvage office desk for the computer. It’s big—60" long and ≈32" deep. That’s practically the last time the top has been seen…
|
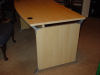 |
|
An end view of the desk, highlighting the depth of the top. Note the grommets for running wires—power cord and data for a monitor or two, power and content for desktop speakers… |
|
My apologies up front—after eight years of documenting my home renovation, one would think I’d have had my camera out, taking pictures, from the earliest stages of this project. One apparently would be wrong. Due to my sloth/indolence/inattention or whatever, you’ve missed the exciting steps of:
- moving the right hand door about 6" to the left to accommodate the depth of the bookcase plus the door casing
- singlehandedly ripping 4'×8' sheets of plywood on the table saw
- truing up stock for the base and uprights
- building the 4" recessed base
- crafting a joint for the lower shelf (because it was ≈13' long)
- dadoing both the lower shelf and uprights for top and intermediate shelves (top shelf in middle bay)
- dadoing for the ½" plywood back panels
- fitting each of the five back panels (all five different dimensions)
- employing a shelf pin jig acquired in 2003 and not previously used, drilling nearly 250 shelf pin holes
- and numerous test fittings of all at several steps along the way
- plus paint.
That’s a lot of stock preparation to get to this point.
Which brings us to…
|
|
|
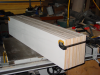 |
|
A stack of plywood ready to be turned into shelves.
| |
|
This stack is shelf stock, nicely uniform in width, ready to be dimensioned for the three lengths needed (each of the three bays is a different width), and for nosing to be applied, and steel bracing to be prepped and installed. Everything was painted manually to this point—then I bought an HVLP sprayer. Oh, how I wish I’d had that for the carcase, which at this point was assembled and installed. Life will not be the same.
|
|
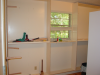 |
|
The skeleton of the bookshelf columns in place. The back panels are ½" plywood and are screwed to the studs. All the shelf pin holes were drilled before painting but aren’t visible in this shot.
|
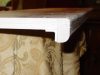 |
|
This image shows the construction of each shelf. Plywood shelf, poplar nosing for strength along the span, rounded over top and bottom.
|
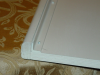 |
|
With shelves on the right nearly 4' long, I decided to brace the nosing with ¾" angle iron—details below.
|
|
First I glued on the nosing (¾" poplar) using biscuits. Then I rounded over the edges—¼" radius on the top to ease the edge, and ½" radius on the bottom to lighten the look of the shelf. A bout of sanding and priming each shelf and I was ready for the steel.
Twelve shelves, twelve pieces of ¾" angle iron, six holes each. Because I’m anal, I did a careful layout by using spacing gauges, depth gauges, and center punches so that each piece of steel was drilled symmetrically and had the same number of screws in each of the three different lengths. The next step was to drill preliminary holes in each piece of steel (twelve shelves × six holes = twelve trips to the drill press).
Mating each piece of steel with a counterpart shelf, and using the steel as a template, I drilled locating holes into the shelves. I knew from experience (my home theater equipment closet shelves) that measuring wasn’t good enough—one needs to template from the item which will be attached. Flipping the shelves over, I then drilled counter bores using the locating holes as a guide. Finally, I bored out the locating holes to accommodate the #10 screws.
The holes in angle iron were then drilled out to the correct body diameter for the tap (10-32) and threaded to take machine screws which would affix the shelf. If you’re keeping score, that’s three trips to the drilling fixture for action on the six holes for each of the twelve pieces of steel—3×6×12 = a lot of pumping the drill press.
|
|
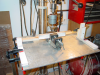 |
|
This is an overall view of the angle iron support fixture. This is the setup for the threading phase—drilling the preliminary holes (and subsequent thread body holes) was done with essentially the same lash up, minus the threading attachment.
|
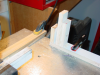 |
|
Detail view of the outboard supports for the angle iron. The tall vertical was added for tapping to counteract the torque of the threading.
|
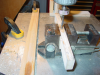 |
|
Closeup of the vise/backing block/tapping fixture used to thread all the holes in the steel. The elongated hole in the block is to accommodate chip ejection from the tap.
|
|
Once all the burrs were cleaned off, I de-greased the steel (lots of thread cutting oil used) and primed them. The shelves having already been primed, I attached each angle iron to its mating shelf and, using a drop of LocTite®, snugged them up. I followed that step by gluing dowels in the counterbores and trimming them flush after the glue set.
After the shelves and steel were assembled, I applied a coat of paint—top and bottom. Along the way, I had thought about routing a sort of mortise on the rear edge near the middle to each shelf to fit all the way back against the back panel instead of sitting proud a mm or so due to the thickness of the shelf support I provided in the middle of each shelf. So, I built a jig…
|
|
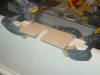 |
|
Jig in place atop rear edge of shelf. Note the pencil marks aligning the jig with the shelf.
|
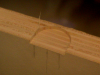 |
|
A resulting mortise.
|
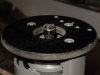 |
|
I got to use my Porter-Cable Trim Router fitted with a flush cut, top bearing bit. The router is upside down for this shot, so the “top bearing” looks like it’s below the cutter.
|
|
Time to work on face frames…
I started with the center section face frame because I wasn’t quite ready to commit to the scribing I needed to do on the outside stiles of the two outside bays. I also wasn’t going to use conventional pocket screw framing, because in order to achieve overall balance, I couldn’t use full size stiles in the center section—they were going to be illusions.
|
|
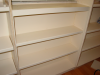 |
|
The finished face frame installed in the center bay.
|
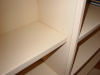 |
|
A closer view of the “phantom”stile—much reduced from what the width will be in the other bays, but still giving the illusion of rail & stile face frame construction.
|
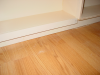 |
|
This shows the detail of the bottom rail as well as the recessed toe space.
|
|
Once the center section was completed, I started to work on the outside stiles which need to be scribed to the wall. A lot of thought went into this from the beginning, as the space to the left of the window ≠ the space to the right of the window. Plus, the shelf space to the right was a little bit wider than 4' so I cheated and made that stile a little wider than the one on the left so I could bring everything back into a single width of plywood (for the back panel, primarily, but it simplified shelf cutting, too).
|
|
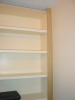 |
|
The right bay, right edge stile, scribed to the wall, and temporarily held in place with two biscuits.
|
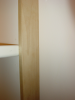 |
|
A closer view of the fit of the stile to the bookcase uprights and the wall.
|
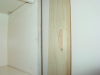 |
|
I’ll use a couple of biscuits on each stile to accurately position the stiles on the sides and against the wall.
|
|
The left bay, left stile has been processed exactly the same way, the only difference being that the left stile is about ¾" narrower than the one on the right. Since the expanse of the bookcase is around 13', no one not knowing about it will pick it up visually.
With those “difficult” stiles fitted, the simple stiles (adjacent to the center bay) can be knocked out easily. Then it’s time to fit the rails (also a simple task), prime, paint, assemble, and I'll be ready to install the face frames. That will complete the book case project.
Toward the above end, today (9 October 2011), I finally got the biscuit slots aligned and cut, and fitted the two simple stiles. I’ve cut the rail stock to rough length, ripped the lower rails to width (2") and have begun the preliminary fitting of rails. In the above description I left out drilling the pocket screw holes (the step immediately preceding “assemble”) which I'll do once I get the rails fitted. So far, it’s a pretty good day, but there won’t be any painting while this hurricane-like rain continues.
A few days later, I had the face-frames fitted, painted, and assembled. A couple of sniggling details and we’re ready for the final push—a big glue up.
|
|
|
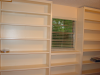 |
|
Voila! These are the finished carcases and shelves. All that’s left to do is install crown (on hand and painted). |
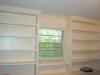 |
|
Done! I know, I know—nail holes to fill, caulk to ceiling…but I can put the tools away, now. |
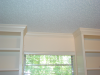 |
|
Closeup of the crown molding. The effect is better than I had hoped for. |
|
31 October 2011—Hallowe’en and Happy 41st. Yesterday was the big glue-up day and the crown got painted. Good thing, too, as today has a nice November-like all day rain. However, due to my prescience yesterday, the crown will go up today in a couple of days (2 November, actually), so essentially this is a finished project. Just in time, too, as our daughter arrived to help us stock the shelves with stuff that’s been sitting in the other bedroom for a while. If I have to hear, “I want to get to my sewing machine,” one more time…
If you have an eye for detail, you might notice a slight anomaly at the top of the two inside case ends. Those are notches I cut to accommodate the crown molding because the stiles of the face frame extend past the vertical members about ¼" (on purpose). When the crown is in, it’ll all blend (cue Marisa Tomei from My Cousin Vinny—“yeah, you blend.”)
See the blinds in the window? Those (and two other sets) were a freebie from a realtor friend. They were apparently for windows about five feet high, but I found a local shade place who cut them down to the 32" height in our windows for just $10 each. They look great.
|
|
| |
|
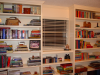 |
Done! Really done. And not a moment too soon. Our daughter arrived the following day for a visit, one agenda item of which was to organize the office. This is what she did.
| |
|
|