Each small picture is a clickable link that will bring up a larger sized picture in a popup screen.
If you keep clicking on images, they’ll appear in the same popup window, so no need to "X" it out until you’re done.
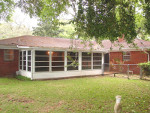
Enclosed porch as we bought it.
|
| When we first bought our house in 2003, the only downside was this fugly enclosed porch installed by the original owners thirty years earlier. It was always a plan to do something with it, and a kernel of a plan developed perhaps ten years ago (≈2006). However, life…
|
Finally, in the Fall of 2016, we connected with a contractor for ideas, confirmation, and ultimately contract, to tear down the old and build anew. To be fair, Hurricane Matthew had folded up a small section of the roof and it was probably repairable. However, if you have a new hammer, everything looks like a nail. Why not start fresh? The project started on 13 February 2017 with demolition.
|
|
| Partway through demolition. They started early, before I even got my sandals on and the phone off the charger.
|
|
| This is how it sat at the end of the first day, bereft of any structure at all. Note the sun peeking over the roof ridge in the west. Footings go in tomorrow, framing to start Wednesday. We’re (bride, Linda, of course, and I) excited.
|
14 February. No pictures on this day, although there was activity. Mostly they poured footings. In the context of this existing concrete pad (actually, two—one over the original), this did not mean a full trench below frostline (hah!) with rebar and forms. No, they basically dug about a half dozen holes—much like post holes and undercutting the existing pad—and poured roughly a bag of Sakrete in each.
A slab-on-grade house (such as ours) is essentially constructed the same way, although there is a trenched, full perimeter footing. Then the slab is poured over it and the ground inside the footer. The purpose of the footings for the Florida Room is to provide more robust support for the old pad which now must support a more substantial structure than the original. Frankly, the second pad we discovered was poured for exactly that same purpose—to support the aluminum enclosure.
Incidentally, note the white streaks on the brick between the door and the window. That’s the swarf thrown off by the K2 concrete saw when they cut a trench (two cuts, two streaks) across the pad. It’s to provide a water diversion away from the new structure. The white thing between the streaks is the permit for the project.
|
|
| 15 February, and the framing got started. There was other ancillary work done before starting with the wood (footings the day before), but it’s a simple structure, so won’t take long. After the last of the deconstruction, preparation for marrying the ceiling/roof to the house, and preparing the French drain for the new North wall. Actually, the first corner studs were put in place before they left on Day 2.
|
|
| Here you can see the framing for the North and South walls nearly done and braced in prep for tomorrow when the east wall gets framed. Off on the lower right you can see chunks of concrete. The previous owner was also a ham and had a self supporting tower at one time. Left in place was at least a yard of concrete and the steel mounting tabs.
I’d thought briefly of putting up a tower when we first bought, but I’ve come to terms that if I ever get active again it wouldn’t be with that kind of tower, so when they rolled out that big jack hammer yesterday for other concrete demo, I asked the contractor if I could make a change order. That pile of debris is his crew making good on it.
|
16 February. Day 4 and the framing is nearly done. When we left off yesterday, the North and South walls had been framed (but not sheathed) although there were details left to do that surprised me. I learned something today, though.
|
|
| This is about halfway through the day, and we have sheathing on the South wall. The big surprise to me was the hurricane anchoring which was done. Each of the three walls has four! ½" diameter threaded rods extending from anchors in the concrete pad, through the bottom plate all the way up through the top plate. This thing ain’t going anywhere! One rod can be seen, but it’ll be too hard to point out in the image when one hasn’t seen it live.
|
|
|
| Here is the end of day shot with a partial finger on the right edge. Damn phone camera! At least I know how to shoot in landscape mode. Almost all the sheathing is up and the jack/trimmer studs are in for the door. The big opening on the left of the East wall has been left unframed and unsheathed to allow easy access from the work shop just out of frame to the left (geez, three “left”s in one sentence, all with different contexts).
|
We’d have been farther along if the load of trusses promised at noon had ever shown up. We’re looking at 0800 Friday, so there’s a possibility we can be dried in for the weekend. Can’t wait to coordinate with the electrician for wiring (perimeter receptacles and power for a ceiling fan). Not sure what the resolution for switches is going to be.
The guys continued cleaning out the rubble from the tower base (not visible in today’s shots) and then diamond wheel cutting off the three stubs and filling in the hole with topsoil (we call it sand in Florida). We got the fence section cleared out, too (after they’d left yesterday) so landscaping will begin within a week, I’ll bet.
The day was capped off by a visit from our tree service guy who in a week or so will dismantle an ailing water oak on the back 40.
|
|
|
| 17 February, Day 5 and the boys earned their keep today. As I told bride (Linda), they call it rough carpentry for a reason. I’ve had some experience myself in this arena, so not only do I understand it, I don’t judge. The trusses were delivered by 0800 this A.M. and they got them “hanging in the attic for curing”.
|
|
|
| The crew finished with the sheathing and then went about setting the trusses. There’s not but six, and it’s a simple matter of “brace the gable truss, set the rest one by one, toe nail them in, then keep them aligned with a furring strip until the sheathing goes on.”
|
But not before framing out the fascia boards and barge rafter. That’s where they ran into trouble. Despite measuring, cutting, and joining to a tolerance of 1/16" or thereabouts, they discovered slight errors of plumb or square that were okay when applying the sheathing, but when aligning the roof framing, need to be more than just close enough. In the pic above, the trusses are in and one of the lads is surveying the effort.
The best description at that point is “Problem Solving 101”, and I’ve been a reluctant practitioner of it all my life. Suffice to say, they spent the bulk of the afternoon fettling the materials to get things back to plumb, level, and square.
|
|
| By the time they were ready to open up the roof of the house and start sheathing, they were out of time. So, we’re not dried in, yet, but Monday morning, we should see some original structure come off and the tying in of the new.
|
|
|
This is how things were left for the weekend. Still, progress.
|
18 February. Not exactly a Porch Project update—more like a filler until work resumes on Monday. Last night we took our plastic porch chairs off the patio and put them in the new porch in order to survey our new domain.
|
|
| This morning, bride (Linda) returned to the scene and settled into one of them while on the phone with friend or family member (it’s a grandchild’s birthday today, so it could have been one of them).
Oh, the apparent graininess in the image is construction dust on the sliding glass door. I had to shoot through it so as not to disturb the candidness of the carefully staged shot.
|
20 February, Day 6?
Uh, on an entirely unrelated, yet necessary housekeeping note, throughout my original series on Facebook, I became aware of a discrepancy creeping in regarding how I was numbering my posts. Preparing this page has illuminated what went wrong and has led to a decision on how to proceed from here.
For the first week, the calendar day and the work day enjoyed a one to one relationship. However, come Saturday the 18th, while the calendar kept incrementing, no work days did. So, on Monday the 20th, it was Day 6 (of work) although Day 8 on the calendar. I'm going to ameliorate things by strictly using the calendar day for succeeding posts, as there really isn’t anything of value in calculating work days.
Even when bride tries to sum up the extent of the project, it’s really only first day/last day which counts, not how many actual work days there were. At the end of the project, it was surprising how few lost work days there actually were. I’m thinking two or three. And, of course, at this remove, it matters not at all.
|
|
| Dried in! Well, almost. When last I reported, the lads had decided not to start opening the existing roof as they would run out of daylight before they could tie in the new roof to the old and protect the structure. So, first thing Monday morning they started attacking the job, removing shingles on the house roof to clear the deck for marrying the new roof to the old (first pic). It was most of the morning getting down to the plywood, then a good part of the early afternoon getting the valley rafters and ridge tied in from the new roof to the old.
|
|
| Following the skeleton, they started laying sheathing, but if you know anything about intersecting roofs (or is that rooves?), you’ll understand it’s not a straight forward “lay down the sheets and hammer them home”. Every course is staggered, so that’s a cut at the gable on every course, and then the other end has to be measured, scribed, and cut to join to the valley framing installed in the morning.
|
|
| Once the framing and sheathing was done, it was time for the vitrethane (or peel-and-stick as the boys are calling it), which is a protective underlayment applied to the new sheathing. By the time they got the valleys protected (valleys are very vulnerable points in the protective shield of the roof) it was time to project the time for the following steps, the need for an inspection before further covering could be applied, and the fact that shingles and drip edge materials were not yet on site. So, they covered what they had accomplished for the day with Visquine and packed it in for the day.
|
My accomplishment for the day was to get a hole drilled in the top plate of the existing wall near the sliding glass door, which allowed me to reroute a length of existing non-mettalic cable (Romex) which will save pulling a new wire for the new porch. This circuit was already dedicated to the old porch, so it’s perfect. I’ll see if the electrician thinks it needs either a GFCI or AFCI breaker. I have another hole to drill in the top plate to get feeds out to the new room—receptacles in the wall, overhead fan, exterior floods at the peak of the gable.
All of that’s in the future, although I did get to meet the mason who’ll be doing the brickwork on the base of the porch. You’ll see.
|
21 February. Well, Generalissimo Franco is still dead, and we’re still dried in. I don’t envy contractors because their life depends on product delivery and the performance of vendors outside of their direct control. And at the same time, they have to keep their own employees working so they don’t starve. Today saw the confluence of several of those stressors.
The beginning of the project was predicated on the issuance of permits (the city’s purview), delivery of the windows (they’re custom and there’s a balance between how long you want to keep a structure open and how long you want to store somewhat delicate product in the weather), securing of both roof shingles and brick which need to closely resemble the existing (and in the case of the brick, 40 year old color, size and pattern), and various other supplies. Lumber came in on time, trusses were late—it’s all a huge balancing act.
So, today was a second inspection by the city and the good news is, he was here early. The bad news is, he was something of a dick, as some inspectors can be. The more good news is his complaints were trivial and easily rectified, and he was soon on his way, his initials gracing the permit. His presence prevented the finishing of the installation of the vitrethane yesterday, and the shingles still aren’t here, and that meant most of what could be done for the drying in was getting the vitrethane installation completed, and get the drip edge on the eaves. Done and done.
|
|
| There were some minor carpentry things that needed attention, so the crew (reduced today) worked on those, while the boss scurried around for things like soffit material.
Then, toward the end of the day, they got the Tyvek (house wrap—air infiltration and moisture barrier) installed.
|
So, windows will (should) be delivered on Thursday, and the door by the end of the week. I’m not sure when the shingles will show up, but a structure like this probably only amounts to a half day’s work for a roofing crew. Think in terms of next week for the mason and the electrician and the trim guys will finish up after that.
I’m sure bride (Linda) would like it done yesterday, but I’m enjoying watching the process. It kind of takes the pressure off me to accomplish other things.
|
22 February. A week and a half of glorious construction weather came to an end today. It started out okay and the crew got a couple of outside things done. The shingles were delivered and conveyored up onto the roof (big boom conveyor—it’s something to see), but either the roofers (sub contractor) weren’t scheduled, or they stepped out onto their porch, threw up their hands and walked back inside (think “Caddyshack”). So, that threw things inside.
|
|
| The electrician(s) came, too, and their job turned out to be just a couple of hours, as I had suspected. Not only that, they were exactly onboard with what I was looking to do, so, check. This is a detail of the wiring on South wall.
|
|
| This one is a detail of where the ceiling fan will go (supported by a brace to handle the fan’s weight), as well as the feed to a floodlight fixture which will be at the peak of the gable on the East face.
|
|
| Once the monsoon started, the boys came inside as there was more piddling carpentry stuff to be done. Here one of them is starting to put cripple studs in to provide structure for the sheet rock which will go between the existing brick and the ceiling.
|
|
| This shows the left of the same partial wall fully studded, or crippled.
|
|
| And this shows the gable wall, the mirror equivalent of the faux gable wall that they had framed yesterday.
|
By 1400, what was left is going to be delivered tomorrow (windows, possibly door). I don’t know the schedule for sheetrock, and I don’t know whether it will be this regular crew or if it’ll be another sub.
Just to keep terms straight, the crew that has been here every day are not subs—they are regular employees of the contractor. And while they’re capable of doing all the jobs in construction, they don’t do the licensed stuff (electrical and plumbing), and they don’t do some of the other specialty trades (roofing and masonry). The roofing sub was just here and we’re told they’re coming Saturday, and, as I thought, it’s a half day job, if that.
We spent part of last evening sitting in the structure and we’ve concluded it’s going to be a dramatic space, far more than the old porch ever was. The ceiling, in addition to the slight vault, is nearly ten feet high. It’s going to be great. Another day closer.
|
23 February. An interim report best expressed as, “some days you win, some days you lose, and some days it rains” (“Bull Durham”).
At least the dry-in inspector showed up and signed us off for shingling on Saturday.
|
24 February. Windoze! Actually delivered yesterday, although I didn’t bother to report it. Amusingly, there were five windows for four holes. One of the sets has tempered glass because of its proximity to the door (code requirement). One of the crew today speculated that they’d probably made four windows, per the order, and then, in a forehead slapping moment, said, “oh, shit, one of those was supposed to have tempered glass!” It was probably more efficient to just make a whole new frame with the tempered glass, and then bundle and ship the five units.
|
|
| This shows the first one being installed,
|
|
| This shot is the outside view. One can also see the ¼" thick, brick width, angle aluminum which will serve as a ledger for the brick veneer (it’s called veneer even though it’s full dimensioned bricks) to be installed up to the level of the bottom of the windows.
|
|
| The above was taken from roughly the same vantage point as the original image which started this thread, shown here, in case you forgot.
|
|
| Whilst awaiting inspections and deliveries, the boys got these cut and attached. This image shows the nicely mitered corner which will be forever entombed under brick and mortar.
|
There are still piddly things to do, or as I call it, more prep. The contractor brought in pieces for trimming the roof overhangs once the shingles are on. Then, fortuitously while he was still here, the inspector showed up for electrical, windows, and final framing inspections. Same dick as before, but it worked out.
Shingles tomorrow, masonry next week (probably), as well as insulation, and interior wall treatment. This concludes two weeks (with one day of rainout). I’m not keeping score on the timeline although someone might be. So far as I’m concerned, it’s going about as it should and in any event, a year from now, we won’t remember if it was done in four weeks or if it took five (ha! it was fewer than six months when we no longer remembered).
|
25 February (Saturday). I was surprised at the arrival of one of the regular crew, as I thought he was taking the weekend off. Maybe he’s making up for the lost Thursday. Anyway, he’s here to start on the soffit/fascia trim.
|
|
| I started to despair on the roofers, but they eventually showed. They wound up spending more time on cleanup and other prep than on actual installation. They stripped back the original shingles to the hip on the South side, I wasn't expecting that. Although our regular guy has been here longer today, the roofers were rocking with very visible results.
|
|
| In this view the north face is probably a quarter done, and there’s nothing to show for our carpenter. In truth, the soffit is fully installed on both the north and east side. You just can’t see it. More below.
|
|
| For a roof that was re-shingled probably eight years ago, the new is a pretty close match. Moreover, hardly anyone will ever be in a position to notice or judge (as this aerial view demonstrates), and I say check back in a year, maybe less, and enough weathering will have taken place to have really blended the product. So check that off as done and done and they’re gone. I'm very pleased.
|
|
| Just to prove there was stuff going on while the roofers came and went, here is our guy installing a piece of fascia on the existing structure. To the right, you can clearly see the soffit material he's installed all around the new porch.
|
27 February. Every day I want to keep saying, “this was a big day,” but when I look back, they all seem to be just small steps in one big parade. Well, the small step(s) today started with the delivery and installation of insulation.
|
|
| The boys did some clean-up first, getting everything that didn’t look like insulation out of the structure, and then proceeding to cut, place, and staple insulation in every nook and cranny. We see the ceiling nearly finished and the wall cavities in progress.
|
|
| This shows the faux gable above the existing exterior wall buttoned up. This view is the opposite direction from the one above. It also dispenses with the brief, attempted colonization of the attic space by some local sparrows. No bird condo in our attic!
|
|
| While the boys were working on the insulation, the boss man hitched up the trailer and hauled all the debris off to be disposed. He then picked up the door and the blue board and upon his return, spotted the trailer again. The lads hauled in the door and drywall and started to work. Here’s an in-progress shot of getting the rock on.
|
|
| And after some Roto-Zip work as well as some drywall screwing, we got to this point at the end of the day. Tomorrow will see completion of the rocking, and then once the “drywall screw inspection” takes place (yes, there is one), the plasterer will come on Wednesday to complete the interior surface.
|
Big day, but still a few to come. Nevertheless, the place is still coming together just as we’d wished.
|
|
| 28 February. Today, the lads finished up the drywall. Here’s a shot of the gable end. The big hole in the insulation is for the installation of a gusset the inspector wanted put in to stabilize the ridge/roof assembly against wracking from forces on the gable itself.
|
|
| You can make out the gusset in this image. Anything that doesn’t look like 2× framing is the gusset. It’s actually plywood, two pieces, important because technically the metal plate forming the joint in the truss is also a gusset. After he got that in, he filled in the last pieces of insulation.
|
The door was also installed, as well as the latch set. The room is not only dried in and rough finished, it’s also secure. General clean up rounded out the day, followed by an application of kraft paper to the floor (temp). That’s to ease cleanup after the notoriously casual work the plasterer does as he’s slinging the mud. That commences tomorrow.
|
|
|
This is taken from the south end of the porch looking north toward the in-law wing of the house. You can see the door, the paper, the walls, and ceiling in this view. That piece of machinery in the middle is a brake, and will be used for forming the termite guard (yes, that’s what I said) next week.
|
You’ll be pleased that the reports are starting to be shorter. I don’t know what you’re going to do when this project is finished.
|
|
| 1 March. Mud! The plasterers (crew of five) showed up fairly early, and got to work. They fine tuned any edges left, then taped all the joints. They got their laborer (junior man on the crew) to start mixing plaster in 5 gallon buckets, and started to work. One man on stilts and the rest from the floor.
|
|
| Sidewalk superintending was ably performed by bride (Linda) as they set about putting on square footage. They worked pretty quickly, but I didn’t spend the whole morning watching, so while I know they typically do three coats (scratch coat, brown coat, finish coat), I can’t testify that they did so here.
|
|
| I also can’t tell what stage this image illustrates, other than there’s product on all the blue board. Also that there a lot of people at work in there.
|
|
| The contract called for a knock down finish, the detail of which you may be able to make out in this image—the left edge shows it best. Please ignore the finger. Grrrr!
|
|
| The last image shows the whole job done and the brake returned to its temporary storage. They were out of here by 1100, which is amazing.
|
I’m told the color will change as the plaster dries. We have yet to select a paint color, and in any event, while it’s possible to paint 24 hours after the plaster is applied, I’m told it’s better to wait a little longer. I suspect we’ll see the paint go on either Saturday or next week.
The only thing we know about paint color is that we’re not going to go bold dark as we’ve done in so many homes both here and in Illinois. We’re probably going toward a lighter shade to reflect the semi-tropical clime here. Also, to maintain the lightness of the room itself.
|
2 March. No actual construction activity to report (and none was anticipated—not sure why, now). Plaster work from yesterday is pretty hard today. Plus, I got out and tackled an ancillary DIY task. The footprint of the new structure is about 20" smaller than the original. The south and east faces remain the same, leaving about that distance of concrete that used to have indoor/outdoor carpet glued to it.
Today, I got busy with adhesive stripper and I think I was successful in getting all the physical adhesive off. Remaining are the stains of the adhesive. When it stops raining, I’ll get out with my angle grinder and try a variety of attachments to attempt to get the stains up. I’ll also attack them with the pressure washer. Not sure which I’ll try first.
Not sure who is scheduled for tomorrow. Could be the mason, but I would have thought the brick would have been delivered today if that were the case. Oh, well. I’m pretty much done now, though—dark and wet.
|
|
| 3 March. No activity to report, but since that’s still something to report, I’ll post this with a picture that belongs to yesterday’s post. I also took some measurements so I can more accurately describe the scope of changes this project embraces. The amount of footprint we gave up (meaning the amount of view through the kitchen window we gained) is 38". From the brick exterior out to the east face is roughly 10’ of inside, usable space.
|
With those numbers in mind, what you see is a 12" trench, a little over 10’ long, and next to it (in the light brown color) is the area of the original structure we gave up and which had indoor/outdoor carpet glued down. The trench will function as a French drain, as three roof surfaces (with two valleys) pour a lot of water into and over the edge of the gutters. It’s also a path to divert said water away from the interior of the new structure. It’ll eventually be finished with a decorative stone (I’m thinking ¾" to 1" river run). Update: We changed the treatment and had the contractor put in pool drain. It’s the perfect solution.
In the meantime, that glue was what I spent my afternoon removing yesterday. Today I can feel that the adhesive really was dispensed with as the remaining concrete is quite smooth. What you can see left is more of a stain (and lack of weathering). In the image you can see a couple of fuzzy dark splotches in the sunlit part. Those are actually shadows from surrounding trees. I suspect a combination of grinding (I’ll try the wire brush head first) and pressure washing will diminish the difference in appearance of the two surfaces. I may have to confront the possibility of an alternative concrete treatment over the whole patio (outside).
Looking ahead, nothing for the weekend, but after talking with the contractor on his morning visit (and to get his trailer for the weekend) we know that the interior will be primed and possibly painted on Monday and the brick will also be delivered on Monday, as well. Tuesday the mason will lay the brick (up to the level of the windows). Wednesday, the full crew should be back to put up the Hardie board and then it’s detail work from there on in, to be completed by next Friday, is the projection.
|
5 March. Even though there hasn’t been a work crew here since Wednesday (Porch Project update 1 March) doesn’t mean I haven’t gotten anything done. When I left you on Friday, there had been the extra window and three sheets of blue board (water resistant sheet rock) leaning against the house (slightly visible in Thursday’s update). It had rained once and some of the rock got wet, but it seemed to live up to its water resistant claim and showed no visible damage after drying out. I moved the rock into the porch and good thing I did, because we had a frog strangler yesterday morning.
Today I wanted to pressure wash the patio, in part to remove the splatter from the concrete cutting the crew did early on to create a trench. I also wanted to see what the difference was going to be between the two areas of concrete, one of which has been exposed since poured, and other which has been covered with indoor/outdoor carpeting for forty years, and off of which I stripped the adhesive on Friday. So, out came the pressure washer.
|
|
| As you can see in the image, it turns out the pressure washer did a pretty good job on the overspray, and it made a slight difference in the glued area, but no amount of effort I can employ will make it all blend. I’m going to find a concrete company that does decorative work and see what they recommend. I don’t think I want a stamped pattern (although I’ll entertain a recommendation if they have a good one). I’m thinking more of a paint (I don’t think stain will be enough) or even an epoxy finish. Fortunately we’re on no time constraint for this aspect.
|
One other thing I got done was to finish stripping the old caulk (visible in today’s image) off the brick where it had been applied to the original structure. I got the bulk of it off (which means it’s probably not silicone) and I’m entertaining ideas of how to remove the residue from the brick. Grinder and steel brush only annoy it.
As a reminder, we’re supposed to get a brick delivery tomorrow, and the mason is supposed to show up Tuesday. More updates to come.
|
6 March. Lots of things, many little, but fun to discuss in some cases. Short list: cedar ceiling lumber was delivered, bricks were delivered, paint selection passed on and delivered, concrete base for French drain was poured, interior was primed, and then…
Paint color was quite the discussion item the last several days. Both of us seemed inclined toward a tropical hue, since it’s essentially a “Florida Room”. That had a different connotation back in the day before the Revolution when my family first moved to Florida. In any event, one of us leaned toward something of an aqua tone, but very light so as not to overpower the space. The other of us was looking more at a coral hue, also quite light, for the same reason.
|
|
| Here’s a likeness of it on the wall. One of us is not as sanguine about her selection as she was when she made it. I am trying to be as supportive as possible, which means not vocalizing anything that’s not positive, which means keeping quiet. The work crew, however, can clearly be heard stifling their giggling.
|
|
| Here is another angle with different light.
|
|
| And this is the view toward the original exterior of the house. Frankly, I don’t think that’s a bad marriage with that brick. In all fairness, we still have the natural cedar ceiling to go in, plus the tile we’ve selected seems to complement the paint a bit. By the time we’ve populated the room with furniture, why, I’ll bet no one will notice.
|
While I’m having a little fun with this, the reality is the painting was in the contract, so at this point we’re really not out anything. Once the crew leaves, we can always go over to Lowe’s and select a different color. We’ll only be out the price of a gallon of paint and some effort. Not like we haven’t expended that before in this house.
Oh, a reschedule on the mason—he’s coming Wednesday instead of tomorrow.
|
7 March. There really wasn’t much going on today except ceiling. It’s simple 4" cedar planking. Most of the morning was spent by the crew in preparation—sanding the product and a few minutes assembling the scaffolding. After all, the ceiling is almost 10’ high at the peak. Then after lunch they got to fitting the two planks at the peak which also included a cutout for the electrical box in place for the future ceiling fan. Yes, there’s an actual ceiling fan support strut spanning the two trusses closest to center.
|
|
| This is a shot of the first few rows of planking.
|
|
| When they’d completed the first half…it was late enough to call it a day.
|
A couple of impressions: First, the aroma. It’s not overwhelming, but you can start smelling the cedar when you’re walking into the dining area on your way out to the porch. Second, as you may be able to tell in the pictures, the consistency of the planking and the color both seem to complement and moderate the wall color. We’re entertaining a vote—there seems to be only two colors of ceiling fans, a brown and a white. Which do you think would be best?
|
|
| Finally, a personal victory. I found a solvent to attack the caulk on the brick left from the original porch structure. You can see in the image that I have four brick cleaned off.
|
The magic is kerosene, about which I’ve long known as the best solvent for cleaning cosmoline off machine tools. It softens the caulk right up. Still some mechanical work with a wire brush, and the kerosene does seem to discolor the brick a bit, but I scrubbed it with mineral spirits, and then some Simple Green. While there’ll probably always be some discoloration, it won’t be the stark white of the caulk, and it may weather out a little bit. I’ll also hit it with the pressure washer when I get all of it cleaned up, and that may help a bit, too. I can’t discount the possibility of some detergent, as well.
|
8 March. Well! All progress to date has been incremental, with only a hint of the future appearance. Today there was some more of that as the boys finished the ceiling, including the molding around the perimeter, as you can see. One of the things we noticed right away, is that there is now a bit of an echo in the room. That’s because everything inside is now a hard surface. All that absorbent ceiling insulation has now been isolated. The room is alive!
|
|
| If ever there was a project that turned out just as you’d wanted, this is it. Who cares about a pink interior when one has this to look at? We’re still awaiting opinions on brown fan vs white fan.
|
|
| I won’t describe other incremental stuff that’s still upcoming, although lets just say we’re definitely in the final stages. The big news is outside. The mason (and his helper) came today. There was the usual standing around, mingling with the other trades, and studying on the details the mason needs to have in order to start the job, as well as some setup. His helper quickly got him a couple of pallets of mortar and several dozen brick staged, and it was off to the races. This shot shows some progress.
|
|
| He didn’t fool around, and got the south wall done by mid afternoon. There were some tricky bits, and it was fascinating to watch him work. Eventually he got the south wall done, including the cap course (that was almost the whole of the tricky bits). This is it complete before cleanup. Among the tricky bits was the termite guard that had to be installed atop the second course. That was bent to order by the lead carpenter as the mason was getting set up. That’s what the brake, which had been cluttering up some earlier pictures, was for.
|
|
|
The mason then got 3½ courses on the long east wall done before it was time to pack up for the day. Here’s a shot of the corner where old meets new. You would have thought the new brick was actually left over from the construction of the original house >40 years ago. We’re stunned. What a transformation from the morning bones to a finished facade (well, partial—the Hardie board has to go on soon). It’s better than we had dreamed, although it’s pretty much what we had dreamed.
|
9 March. Half of the action today was kind of invisible. By deduction, that suggests the other half was not. The first case involved, well, casings, as well as other trim in the interior. For all that got done—ceiling trim, door casings, brick trim, and baseboard—I can’t produce an image, because there’s still a fair amount of clutter in the room. I promise an image soon, but take my word for it now. Oh, and another aspect of the invisibility was that much of the trim needed painting first. I didn’t think you needed a picture of painting.
|
|
| On the brick front—literally, the brick front—the mason got working straightaway on the long east wall. Here he is early in the day, about halfway up the wall. The staging is three sections of planking with three pallets of mud, plus piles of brick, all replenished by his helper while he does nothing but lay brick. It’s fascinating to watch, but it must be tedious and tough on the back on the lower courses.
|
|
| This shows the east wall essentially complete, with the cap course done, or nearly so. By the time he left, he had about three courses on the north wall done, but hadn’t moved the staging, so I didn’t get a big picture shot of the east wall. Trust me, it’s even more stunning than yesterday’s result. There was some drama involving some discrepancy in the level of the four windows, but it seems the mason was able to massage the installation to accommodate. I won’t be able to judge until the north wall is done and the staging has been removed.
|
On another, less result oriented, front, the Hardie board was delivered, so I look for some siding to go up on Friday. That, too, needs painting, another process I’ll likely not record. For my part, I got the caulk, reported in an earlier episode, cleaned off the house brick. I need to do a little de-greasing and probably pressure washing, but it’s already 100% improved.
|
|
| Addendum: I didn’t realize what the carpenter had been doing on the south wall while I was concentrating on what the mason was doing on the east wall. Here’s a look at his work. Some of it will be buried and will never be seen again. On either side of this image is the Hardie board corner board and trim for the window, in between and hard to see is a piece of painted aluminum with a bend which serves as flashing behind the siding and over the brick cap. Nicely done all around.
|
We’re close. The mason will finish today.
|
10 March. The mason finished up today, and I can only reiterate what I’ve been saying for two days—spectacular! The brickwork looks like it was part of the original house, built in 1973. Here are some images while the mason was working. In addition to his efforts, the carpentry crew were at work, as well. Yesterday’s update highlighted the initial efforts at installing siding. Today, they got much farther along.
|
|
|
| Okay, the first image shows the north wall with all but the final course laid. Although it sort of looks like the wall is curved at the outside corner, it’s not. That’s an optical illusion created by the cap course on the east wall, a piece of plywood on the lawn halfway to the carpenter and his saw horses, and the pile of mortar on the staging. Very confusing.
|
|
| The next course, the cap course, which is much like the chair rail on wainscoting in an interior wall, is being installed in this image. The difference in tone in the brick is that the east wall is dry, having been laid yesterday. The work behind the mason was mostly laid today, and thus the mortar is wet and there’s moisture on the brick from the process.
|
|
| The wide view in this image shows the north and east wall with the brick complete. You can also see that the siding, as well as the window trim has been installed up to one course into the gable. They ran out of material, so they’ll finish that up on Monday. The north wall also gets the casing and siding treatment, but, as you can see, there’s not much to put up. I should add, that’s not the finish color—it’s just how it came (primed) from the distributor. Color comes next week, too. Probably just a white.
|
|
| Finally, the last image shows just what this mason was worth. In addition to building the small brick column to the right side of the door, he also built a threshold in the same manner as the cap all around the rest of the brick work. It’s that finishing touch that really defines the brick job.
|
You can also see more closely where there had been the vertical line of caulk from the old structure. I’ve gotten the caulk all off, but the mineral spirits have left a bit of stain, as well as not getting the soaked in caulk completely out. This picture makes it look worse than it really is, but I’m planning (after having tried Formula 409 today) on having a go with a TSP wash (tri-sodium phosphate), and if that doesn’t work, I’ll get medieval with it and use muriatic acid. The mason says that cures most brick ills. I’ll still pressure wash it at the end.
The punch list for next week is really short.
|
|
| 11 March. No construction activity on site, but bride (Linda) and I went to a lighting store nearby and picked out and ordered a fan. On the way back home we stopped at a tile store with whom we’ve done business (powder bath floor tile) and ordered the tile from the sample we’d brought home earlier.
|
Both are projects I’m tackling, so when the construction crew packs up their old kit bags next week, I’ll still have those left to do. I’ll quit counting Days when they do, but I’ll update you when the other activities are completed.
|
13 March. Although there was threat of as well as actual sprinkles off and on, we had a one man army on site today. He finished off the siding including a minor change I asked him to execute. He would have liked to paint, but the humidity too often bumped against the 100% mark, so he settled for the siding and then general organization and clean up with a view to vacating the site after tomorrow’s work.
|
|
| The first image is the same oblique, NE to SW view I’ve shown of the whole structure except now it’s essentially complete. Siding needs painting, so don’t think that ochre is the final color.
|
|
| The second image shows the door and the change I asked for. The carpenter had run a piece of flat molding vertically on the right side of the door. I thought it looked odd, although I understood why he did it. But the width of the space was not much different from the space on the left side of that window (not seen here. but you might be able to make it out in the first image), And I thought it would look better with claps in there. He accommodated me and I’m glad we agreed on it. It looks right.
|
The lamp you can see inside has been put out and brought back in for the last week as we’re excited to see how it feels in there with the cathedral cedar ceiling and the big windows. When bride (Linda) turned it on last night, the bulb popped, so when we went over to the big box to get the outside flood light fixture for the gable of the structure, I picked up a couple of LED bulbs and replaced the spare we’d put in last night. It really looks nice.
I’ve transitioned to LEDs for some time now. Yes, they’re more expensive than incandescent, but the prices have plummeted precipitously. There are at least two off setting advantages, however—heat, or more exactly, lack thereof. The second is efficiency. They cost very little to operate, and a household wide change will make quite a dent in the electric bill. I put four of them in bride’s vanity mirror, and you couldn’t ask for better light, plus she can leave them on (absent mindedly or not) as long as she wants.
On tomorrow’s agenda is paint, a little concrete work for the drain at the base of the north wall, and clean up and abandonment. Two other trades need to finish up (electrician and gutter guy) but they’re not on the carpenter’s schedule.
|
14 March. Last contractor day in the project. Painting is complete. Gutters are installed. Pool drain is concreted in. Still to come, the final electrician visit, plus my projects: tile and fan, neither of which can even get started until next week. I’ll probably post a finish shot of those two aspects later on.
|
|
| Finally, the next two images show details of the north wall finished today. First is the overall of the north wall taken on that same NE/SW perspective. You can see that the trench has been filled in and a drain has been set in the concrete.
|
|
| The last image shows better detail of the drain and also more contrast in those claps on the left which might not have been clear with yesterday’s view.
|
Nevertheless, at the very least, all of the tools, materials, and scrap have left the building, we’ve said goodbye to the workers, and we can begin the planning process regarding furniture and appointments.
|
|
| In addition to this final image, I’d like to address something which served as a significant driver to this project but has gone heretofore undocumented—the view from the kitchen.
|
|
| This picture was taken about ten years ago. As you can see, the old porch structure imposed considerably on the view. The brick of the opposite patio wall (out of view to left) does, as well, but that’s not going anywhere, so there’s nothing to be done.
|
|
| This image shows the view through the window today. It’s immensely improved and psychologically alters the entire feeling while standing at the sink. We no longer feel like we’re looking out through a tunnel. I spoke earlier about the increased patio space, which also has an effect on the perception of the space, but the resultant window view is what really makes the project worthwhile and wholly satisfying.
Curiously, although we’ve given up more than two feet (≈20’2) inside the Florida Room, between the junk which is no longer stored there and the vastly increased ceiling height (plus the vault), it feels like a much bigger room than before.
|
Thanks to all of you who followed along. I hope you’ll be able to experience it in person at some point.
|
Coda: Below are a few follow up shots which are complementary to, yet distinct from the porch construction.
|
|
| This is the fan we bought and installed. Intentionally shot at a speed low enough (and without flash) to give the impression of moving, which it is. It has 60" blades, which we were originally concerned might be too big for the width of the room, but up in that vault, it’s just the right size. It has three speeds (we’ve settled on medium), and it’s reversible (we’ve settled on updraft). We usually have it on 24/7. It’s sooooo quiet.
|
|
| This is the back yard illuminated by the motion sensor security lights high in the peak of the new gable. You saw reference to it a couple of times and may have wondered at its import. It should come as no surprise they’re LEDs. This should do the job.
|
|
| We’ve always had a security light over the slider across from the porch, and the carpenter had it out for a while to do soffit reconstruction when finishing up the Florida Room. I saw the opportunity to replace it, not only so I could get an LED light there, but so I could eliminate the motion sensor aspect. With the big triple fixture on the gable end of the porch, there’s no need for that feature here, which makes it a handy BBQ light.
|
|
| Preparing for setting tile is often a complicated process, even for so simple a space as this. I’ll spare you the details. However, I will share this one shot part way through the job.
|
|
| We’re quite pleased with the tile. Not only as a stand alone element, but to paraphrase “The Dude”, it really ties the room together. That wall color we chose, plus the brick, as well as the cedar on the ceiling, the white trim…even the white fan (although you can’t see it here) all seem to work together, at the same time toning down elements of the others, while adding its own subtle charm. A brown leather love seat has since been added, providing its own contribution. We’re pleased.
|
|
| One final note. Some months after finishing the Florida Room, and enjoying it daily, bride got the idea of expanding our patio. We might have been inspired by our neighbor putting in a new driveway—replacing the old concrete with new pavers. So, she sought out a contractor, agreed on a price, and in a half day’s work, we got this.
|
It’s less for actual function—unless we put on a large garden party—as it is to enhance the backyard, which has been, heretofore, unremarkable. BBQ will still be on the original patio, and we’re not even sure we’ll populate it with furniture. Sure looks nice, though
|